プリント基板(PCB)の外観検査は、プリント基板の製造工程で品質を保証するプロセスです。微細な欠陥や異常が製品全体の性能に大きな影響を与える可能性があるため、正確な検査が求められます。本記事では、PCBの外観検査のポイント、タイミング、そして自動光学検査(AOI)を使用した外観検査まで詳しく解説します。プリント基板の外観検査についての知識を深めて、適切な外観検査の方法を検討していきましょう。
プリント基板の外観検査をする理由
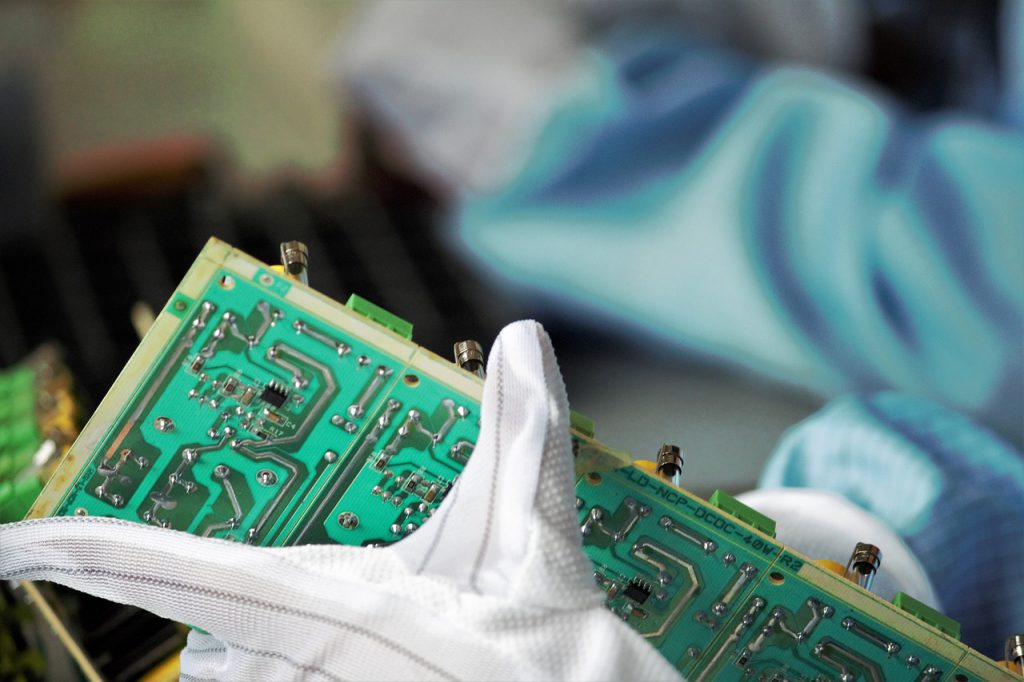
プリント基板(PCB)は、電子機器の心臓部ともいえる重要な部品の一部です。そのため、製造プロセスにおいて外観検査は必要なステップとなります。
外観検査を行う理由の一つは、製品の品質を保証するためです。製造過程で発生する微細な欠陥や不良は、最終製品の性能や信頼性に大きな影響を及ぼす可能性があります。例えば、微小なクラックや異物混入、配線の断線などがある場合、電気的なショートや信号の途絶が発生し、最終的には機器の故障や動作不良を引き起こす可能性があります。
また、外観検査は生産効率の向上にも寄与します。早期に欠陥を検出することで、不良品の発生を防ぎ、再加工や廃棄コストを削減することができます。これにより、プリント基板の製造コストの削減が実現します。
こうした理由から、プリント基板の外観検査は、品質保証と生産効率の両面で重要な役割を果たしています。
プリント基板の構造
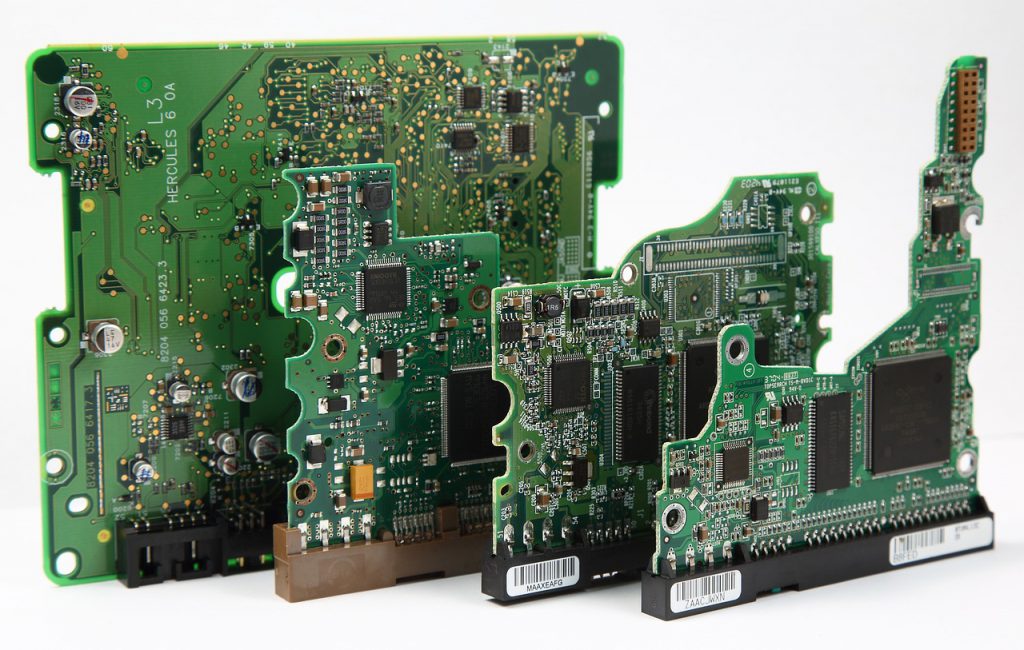
プリント基板(PCB)の構造は複数の層で構成されています。そして、各層は特定の機能を果たします。以下では、PCBの主要な構造要素について詳しく説明します。
絶縁基板
絶縁基板は、プリント基板の基本となる部分です。絶縁基板は通常、ガラス繊維をエポキシ樹脂で固めたFR4と呼ばれる素材で作られています。絶縁基板は、電気的に絶縁されていることが重要で、これにより基板上の異なる電導パターンがショートするのを防ぎます。また、絶縁基板の機械的強度や耐熱性も重要な特性であり、この特性によりプリント基板は過酷な環境でも安定して動作します。他にも織りガラスファブリック表面と紙コアとエポキシ樹脂との複合材料であるCEM-3などの材料もあります。
電導パターン
電導パターンは、プリント基板上で電気信号を伝達するための銅箔で形成された配線です。これらのパターンは、基板の設計図に従い、エッチング技術を用いて作成されます。電導パターンは、電子部品間の接続を実現し、信号の伝達や電源供給を行います。パターンの幅や間隔は、信号の特性や電流容量に応じて設計されます。高密度なPCBでは、複数の層に渡る多層基板が使用され、各層の電導パターンはビアホールと呼ばれる穴を通じて接続されています。これにより、複雑な回路構成が実現可能となります。
レジスト層
レジスト層は、プリント基板の表面を保護するための絶縁コーティングです。このレジスト層は、基板の電導パターンを酸化や腐食から守り、短絡の防止にも寄与します。また、レジスト層はハンダマスクとしても機能し、ハンダブリッジの防止や部品の正確な実装のサポートもします。さらに、レジスト層にシルクスクリーン印刷を施すことで、部品の識別や取り付け位置を表示することも可能です。
プリント基板の製造工程と外観検査のタイミング
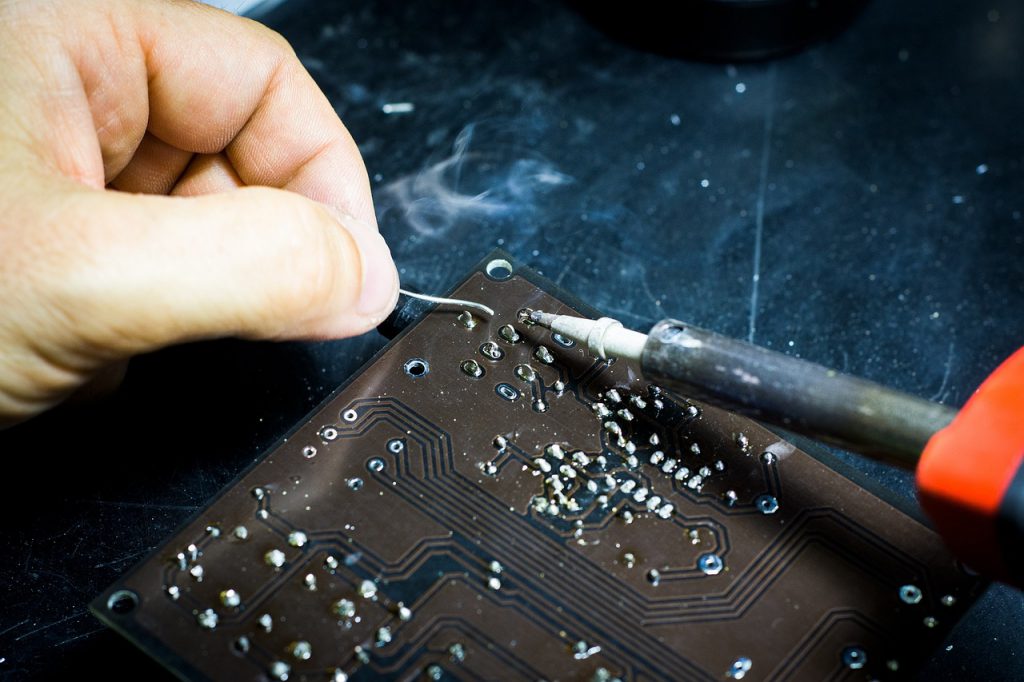
プリント基板(PCB)の製造工程は、多くのステップを経て行われ、工程の途中での外観検査が重要な役割を果たします。以下に、PCBの製造工程と外観検査のタイミングについて詳しく説明します。
材料カット
製造工程は、絶縁基板材料のカットから始まります。FR4などの基板材料を必要なサイズにカットし、次の工程に備えます。この段階では、材料の表面に傷や汚れがないかを目視検査で確認します。
内層パターン形成 自動光学検査(AOI)
カットされた材料に、内層パターンを形成します。銅箔を基板にラミネートし、フォトレジストを塗布して、露光とエッチングを行い、回路パターンを形成します。内層パターン形成後、AOI(自動光学検査)を実施し、パターンの欠陥や不良を検出します。
積層
内層パターンが検査された後、複数の層を積み重ねる積層工程に進みます。内層間に絶縁材を挟み、加熱と圧力をかけて一体化します。この工程で、層間の接着不良や異物混入がないかのチェックも後に実施します。
穴あけ加工・スルーホールめっき
積層された基板に、ドリルでスルーホールを開けます。この穴は、層間の電気的接続を確保するために必要となります。穴あけ後、スルーホールをめっきし、導電性を持たせます。
外層パターン形成 自動光学検査(AOI)
スルーホールめっきが完了したら、外層パターンを形成します。内層パターンと同様に、銅箔をラミネートし、フォトレジストを使って露光・エッチングします。この段階でもAOIを用いて外層パターンの検査を行い、欠陥や不良を確認します。特に外層は、電子部品との接続に直接関わるため、非常に重要な検査ポイントです。
レジスト・シルク印刷
外層パターンが形成された後、レジスト層を塗布します。レジストは基板を保護し、不要な部分にハンダが付着するのを防ぐためです。また、シルク印刷で部品番号やマークを基板に印刷します。
外形加工
基板が完成したら外形加工を行い、最終的な形状に切り出します。この工程で基板の端部にバリや欠けがないかを後に目視検査します。
最終検査・出荷
全ての工程が完了した後、最終検査を行います。ここでは、外観検査だけでなく、電気的検査も行い、基板が設計通りに動作するかを確認します。最終検査に合格した基板は、梱包されて出荷されます。
プリント基板の外観検査の不良ポイントは?
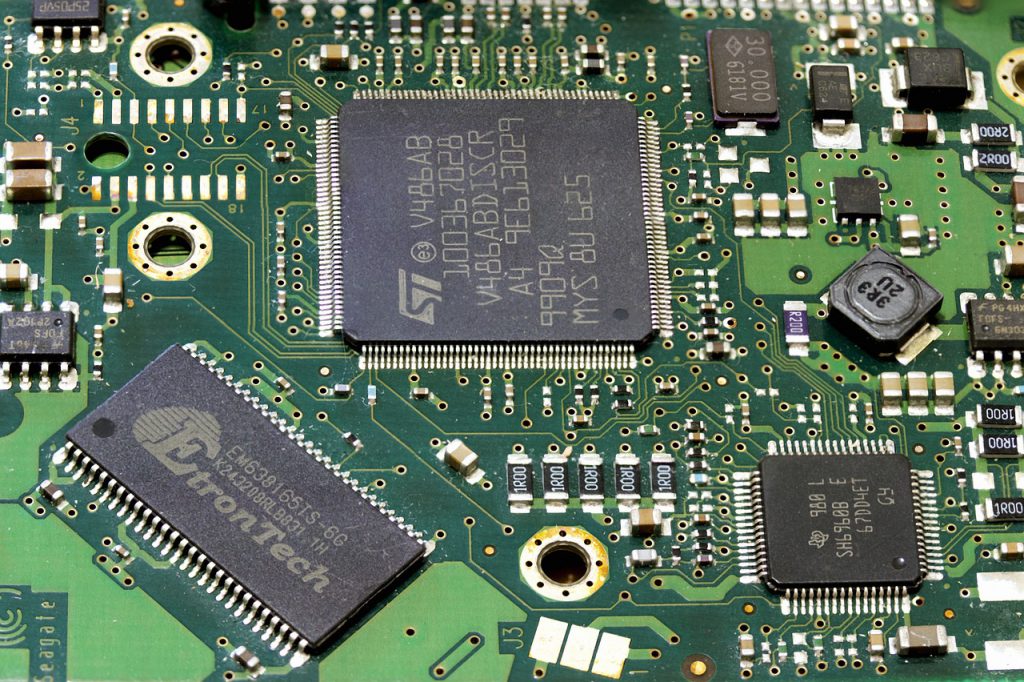
プリント基板(PCB)の外観検査では、様々な不良ポイントがチェックされます。これらの不良は、製品の性能や信頼性に直接影響を与えるため、早期に発見し対処することが求められます。以下に、代表的な不良ポイントについて詳しく説明します。
回路のショート・オープン
回路のショート(短絡)やオープン(断線)は、PCBの重大な不良ポイントです。ショートは、異なる回路が意図せず接触し、電流が誤った経路を通る状態を指します。これにより、デバイスの誤動作や破損を引き起こす可能性があります。また、ショートは主に、エッチング不良や異物の付着、レジスト層の不備などが原因で発生します。
一方、オープンは回路が途切れ、電流が流れなくなる状態を指します。これもまた、デバイスの正常な動作を阻害します。オープンは、配線の断線やスルーホールの不完全なめっきなどが原因で発生します。
欠陥(傷・割れ・欠け)
基板表面の欠陥も不良ポイントです。傷や割れ、欠けなどは、基板の機械的強度を低下させ、最終製品の品質に悪影響を及ぼす可能性を高めます。これらの欠陥は、製造工程中の機械的ストレスや取り扱いミスによって生じます。
汚れ・異物
基板表面の汚れもまた、外観検査のチェックポイントです。汚れには、製造過程で付着したダスト、油脂、フラックスの残留物などが含まれます。これらの汚れは、基板の電気的性能に悪影響を及ぼし、ショートやオープンを引き起こす可能性があります。外観検査では、基板表面の清潔さをチェックし、必要に応じて再清掃が行われます。
プリント基板の外観検査を目視で行う問題点
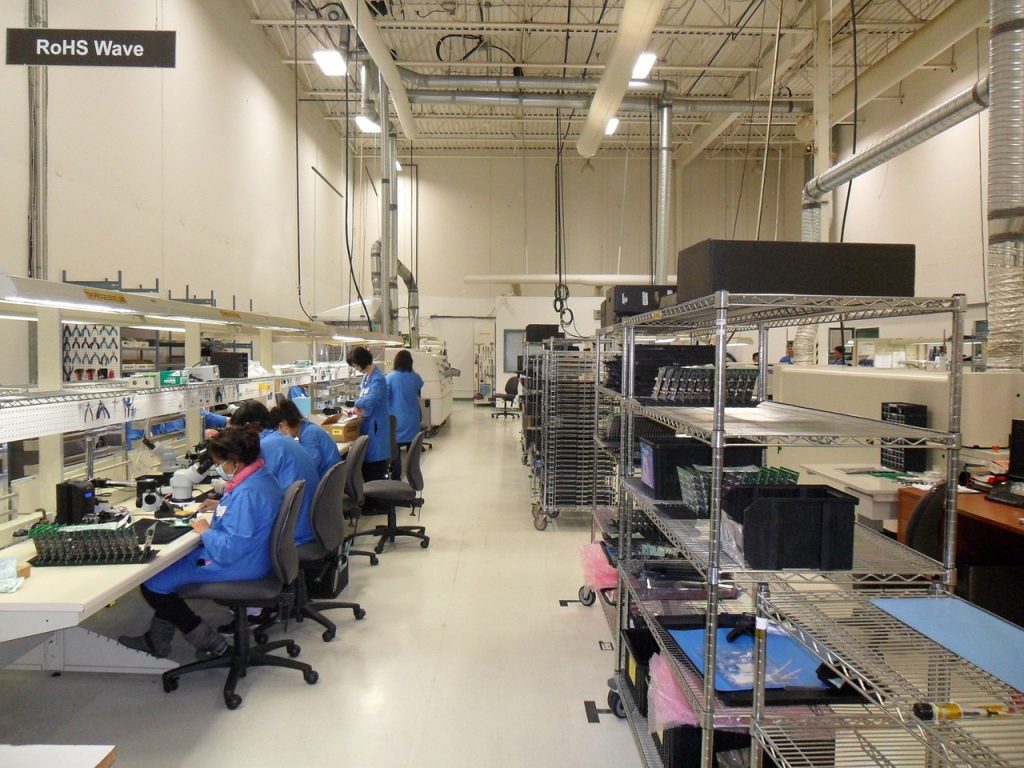
プリント基板(PCB)の外観検査は品質を確保するために不可欠ですが、目視による検査には多くの問題点が存在します。ここでは、目視検査における主要な問題点について詳しく説明します。
検査時間がかかる
目視検査は非常に時間がかかります。熟練した検査員が一枚一枚の基板を細かくチェックするため、大量生産の現場では特に問題となるでしょう。自動化された検査システムに比べて、目視検査は人間の目と手による限界があるためです。
また、検査員の疲労も時間がかかる原因の一つです。長時間にわたって集中力を保つのは困難であり、疲労が進むにつれて検査スピードが低下し、見逃しやミスが増える可能性があります。
検査精度が低い
目視検査は人間の視覚に依存しているため、検査精度に限界があります。微細な欠陥や不良を見逃すリスクが高く、特に高密度な回路や複雑な基板ではその傾向が顕著です。検査員の経験や技能に大きく依存するため、個人差が生じることも問題です。熟練した検査員でも、微小なクラックや汚れ、配線の断線などを完全に検出するのは難しい場合もあります。
検査コストがかかる
目視検査はコストが高いという問題もあります。検査員の人件費が主なコスト要因となり、大量の基板を検査するためには多くの人手が必要です。また、検査員の教育やトレーニングにも時間と費用がかかります。目視検査を行うためには、専用の検査スペースや適切な照明環境も必要となり、これらもコストに含まれてしまいます。
プリント基板の外観検査は自動光学検査(AOI)が効率的
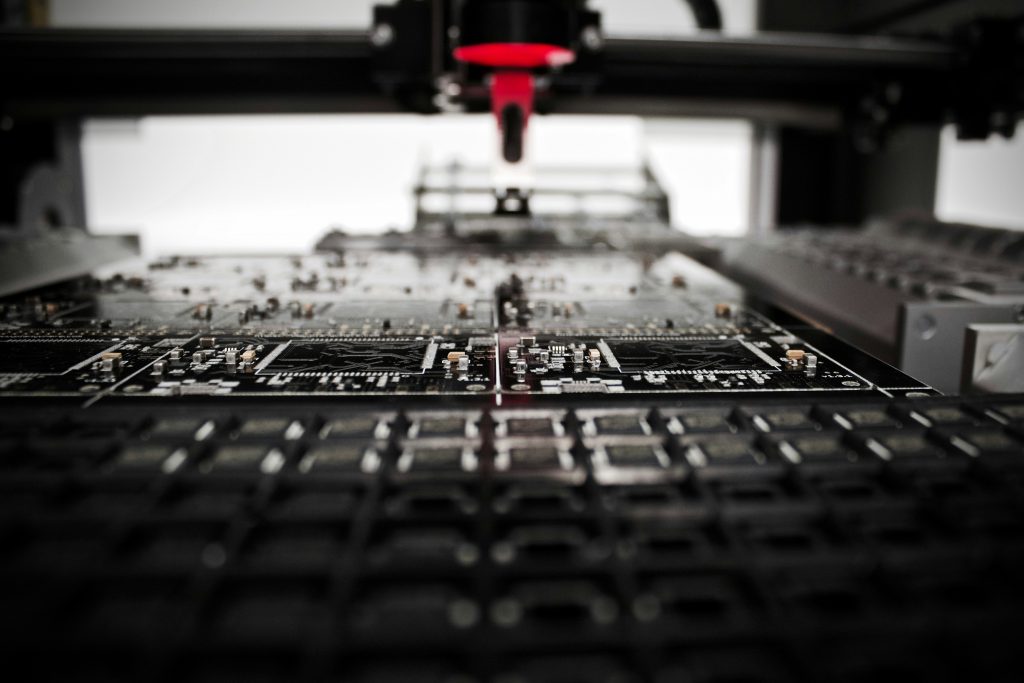
プリント基板(PCB)の外観検査において、自動光学検査(AOI)は非常に効率的で効果的な方法とされています。AOIは蛍光、紫外線、LEDなどの異なる光源のカメラシステムを使用して連続画像を撮影し、その画像を処理して欠陥を検知する検査機です。AOIの導入は、従来の目視検査に比べて多くのメリットを提供し、製造プロセス全体の品質と効率を大幅に向上させます。
以下にAOIを使用したプリント基板の外観検査のメリットを解説します。
検査精度が高い
AOIは高い精度と信頼性を誇ります。高解像度カメラと高度な画像処理アルゴリズムを組み合わせることで、微小な欠陥や異常を正確に検出することが可能です。これにより、人間の目では見逃しやすい微細なクラックや短絡、断線、異物混入なども発見できます。さらに、AOIは検査基準を統一しているため、一貫した品質管理が可能です。これにより、検査員の経験やスキルに依存しない安定した検査結果が得られます。
検査時間が速くなる
AOIは検査速度においても優れています。自動化されたシステムは、高速で連続的な検査を実現し、大量生産に対応することができます。これにより、全体の生産効率が大幅に改善されます。
費用対効果が高い
AOIは初期導入コストは高いものの、長期的には人件費や再検査コストの削減が期待できます。自動化による高い検査精度とスピードは、品質管理の手間を減らし、不良品の発生を抑えることで総合的なコスト削減につながります。
まとめ
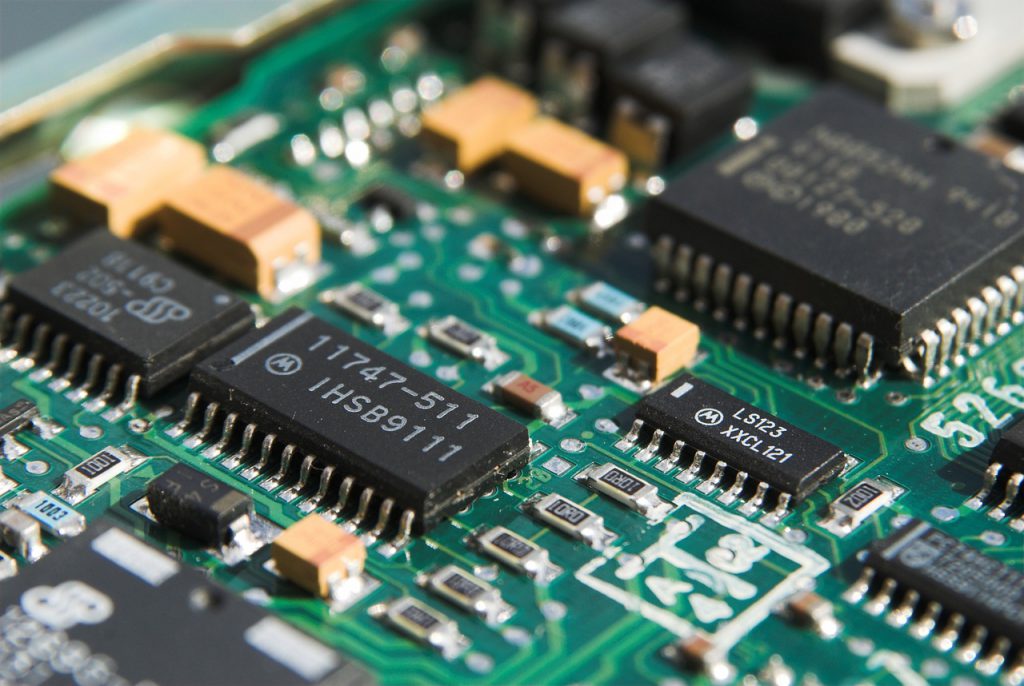
プリント基板(PCB)の外観検査は、プリント基板の製造工程において品質保証の重要な役割を果たします。微細な欠陥や異常が製品全体の性能に影響を与えるため、正確な検査が不可欠です。また、従来の目視検査の問題点として、検査時間の長さ、精度の低さ、コストの高さが挙げられますが、AOIの導入によりこれらの問題を解決できます。
Phoxterでは、条件にあったプリント基板の外観検査装置をご提案することができます。新規の装置の検討はもちろん、すでに導入されているプリント基板装置に対して、当社のStellaController2.0を追加実装することで、大きな改造なくAIによる検査の自動化ができるケースがあります。
お困りごとがありましたら、まずはPhoxterまでお気軽にお問合せ下さい。
お問い合わせ先:CONTACT – Phoxter Corporation