現代の製造業では、ワイヤーハーネスが自動車や電子機器の信頼性を支える重要な役割を担っています。しかし、品質管理が十分でなければ、最終製品に深刻な問題を引き起こす可能性があります。そのため、ワイヤーハーネスの外観検査は、ワイヤーハーネスの製造プロセスにおいて欠かせない工程となっています。
この記事では、ワイヤーハーネスの外観検査の目的から始まり、ワイヤーハーネスを構成する部品、具体的な検査項目、検査手法について詳しく解説します。さらに、従来の目視検査の課題を克服するために注目されている画像検査のメリットについても触れます。
ワイヤーハーネスの外観検査についての知識を深めて、適切な外観検査の方法を検討していきましょう。
ワイヤーハーネスの外観検査の目的
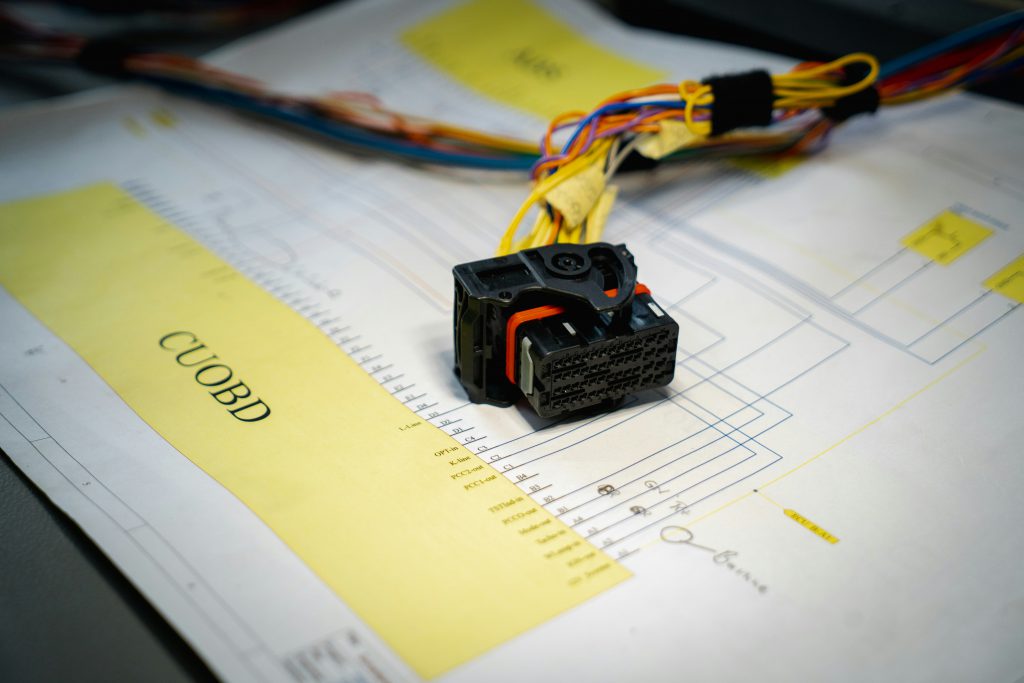
ワイヤーハーネスは、自動車や電子機器などの様々な製品で使用される部品です。その品質が製品の信頼性や安全性に直結するため、ワイヤーハーネスの外観検査は欠かせない工程となっています。外観検査の目的を理解することで、その重要性がさらに明確になります。
まず、外観検査はワイヤーハーネスの製造過程において発生する不良や欠陥を早期に発見し、製品の品質を確保するために行われます。具体的には、配線の断線、接続部の不良、絶縁の不備などが検査対象となります。これらの欠陥は、最終製品の動作不良や安全性の問題を引き起こす可能性があるため、外観検査を確実にすることが求められます。
ワイヤーハーネスを構成する部品
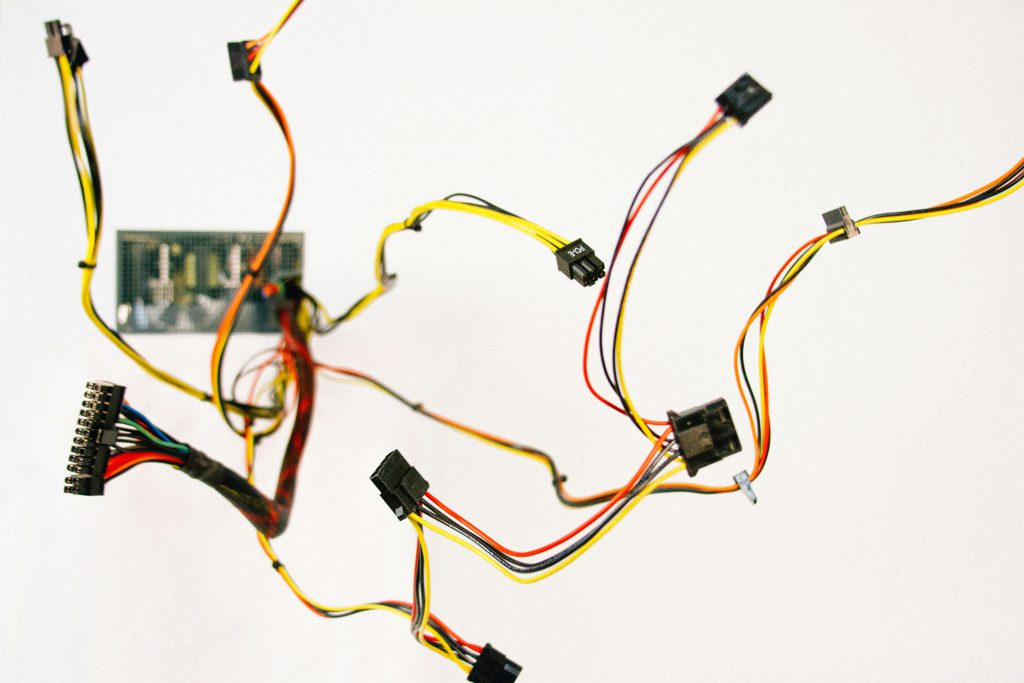
ワイヤーハーネスは、複数の部品から構成されており、それぞれの部品が特定の役割を担っています。以下に、ワイヤーハーネスを構成する主要な部品を紹介します。
電線
電線はワイヤーハーネスの基本的な構成要素であり、電力や信号を伝送する役割を持ちます。電線の材質や太さ、絶縁体の種類などは、用途や要求される性能によって異なります。高品質な電線を使用することで、電気的な信頼性と耐久性を確保することができます。
ハウジング
ハウジングは、電線を接続するためのコネクタ部分を保護するカバーです。ハウジングは、接続部の信頼性を確保し、外部からの物理的なダメージや環境要因から電線を保護します。また、接続部が正確に配置されるようにガイドする役割も果たします。
チューブ
チューブは、電線を束ねて保護するためのカバーです。チューブは、摩耗や引っ張り、熱などから電線を守るために使用されます。特に、エンジンルーム内や車両の床下など、過酷な環境で使用されるワイヤーハーネスには耐熱性や耐油性の高いチューブが必要です。
クランプ・結束バンド
クランプや結束バンドは、ワイヤーハーネスを固定し、配線が適切に配置されるようにするための部品です。これらの部品は、ワイヤーハーネスが振動や動作中に動かないように固定し、配線の整然とした配置を維持します。これにより、配線の摩耗や断線を防ぐことができます。
テーピング
テーピングは、電線を束ねたり、特定の部分を保護するために使用されます。テーピング材は、絶縁性能や耐熱性能が高く、電線同士の摩擦や振動による損傷を防ぐ役割を持ちます。また、防水性を持たせるために使用されることもあります。
端子
端子は、電線の末端に取り付けられ、電気的な接続を確立するための部品です。端子は、圧着、はんだ付け、圧接などの方法で電線に取り付けられます。
ワイヤーハーネスの外観検査項目
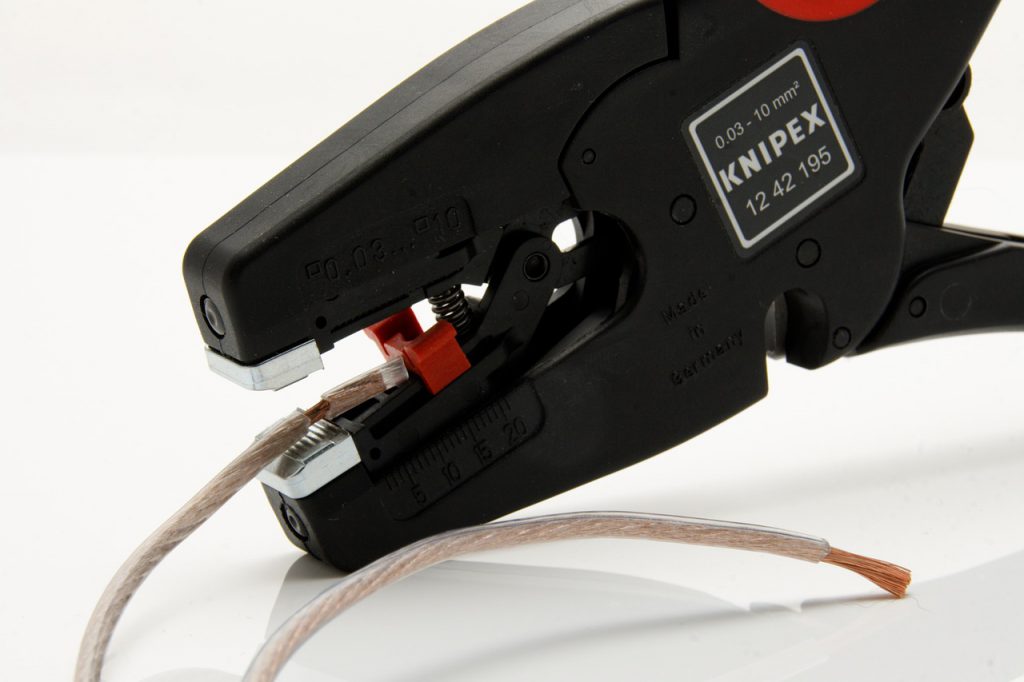
ワイヤーハーネスの外観検査では、多くの項目がチェックされます。これにより、製品の品質を確保し、欠陥や不良を早期に発見することができます。以下に、主な外観検査項目を詳しく説明します。
カシメ(圧着)
カシメ(圧着)は、電線と端子を強固に接続するための方法です。圧着部分の外観検査では、適切に圧着されているか、圧着部分に異常がないかを確認します。圧着不良は接触不良や断線の原因となるため、圧着工具の状態や圧着条件の確認も重要です。また、圧着部分の形状やサイズが基準を満たしているかもチェックします。
圧接
圧接は、電線と端子を機械的に結合する方法であり、主に車両や産業機械で使用されます。圧接部分の外観検査では、圧接が均一に行われているか、圧接部分に隙間がないかを確認します。圧接不良は電気的な接触不良や機械的な強度低下を引き起こす可能性があるため、圧接機械の調整や定期的なメンテナンスが必要です。
はんだ付け(ろう接)
はんだ付け(ろう接)は、電線と端子を金属の融点を利用して接続する方法です。はんだ付け部分の外観検査では、はんだが均一に流れているか、気泡やクラックがないかを確認します。不適切なはんだ付けは、接触不良や耐久性の低下を引き起こすため、はんだの品質やはんだ付け条件の管理が重要です。また、はんだの過不足やフラックスの残留もチェックします。
寸法検査
寸法検査では、ワイヤーハーネスの長さや部品間の距離が設計図通りに作成されているかを確認します。寸法が不正確な場合、組み立て時に問題が発生する可能性があります。特に、自動車や航空機などの複雑な配線が求められる分野では、寸法の正確性が極めて重要です。寸法測定には専用の測定器具を使用します。
部品組付
部品組付の外観検査では、電線、端子、ハウジングなどの各部品が正しく取り付けられているかを確認します。部品が正しい位置に配置されているか、部品の欠損や破損がないかもチェックします。組付不良は、後工程での問題や最終製品の不具合の原因となるため、正確な検査が求められます。また、各部品の取り付け角度や方向も基準通りであるかを確認します。
ワイヤーハーネス外観検査の主な手法
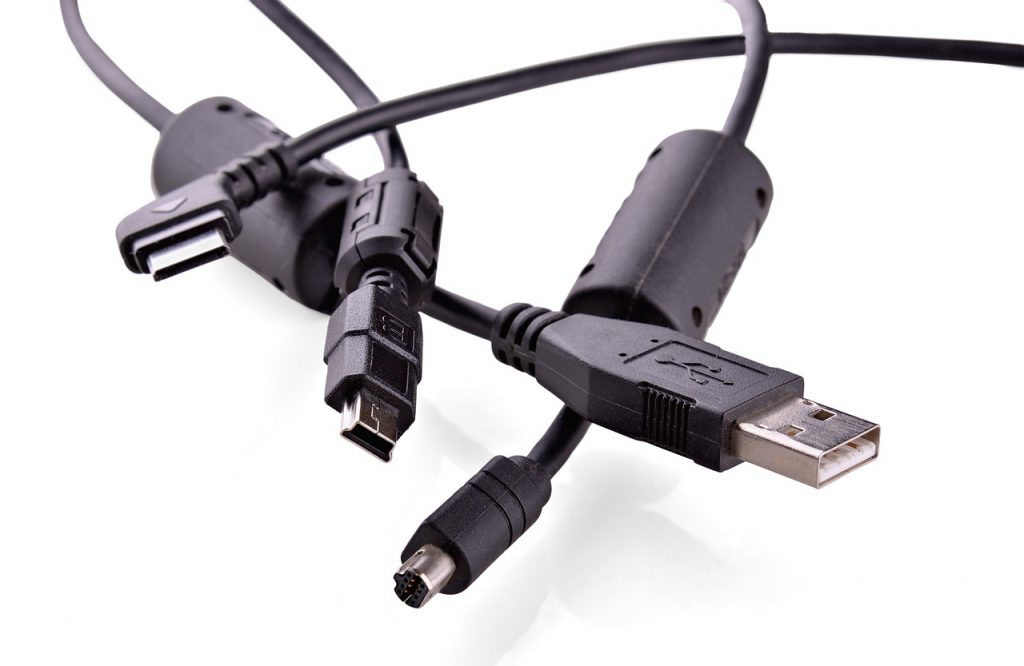
ワイヤーハーネスの外観検査には、様々な手法があります。ここでは、代表的な検査手法を紹介し、それぞれの利点と課題について説明します。
目視検査
目視検査は、最も基本的な外観検査方法です。熟練した作業者が目視でワイヤーハーネスをチェックし、欠陥や不良を発見します。この方法の利点は、柔軟性がある点です。目視検査は特別な装置を必要とせず、作業者の経験と技能に依存します。しかし、目視検査にはいくつかの課題もあります。人間の目には限界があり、微細な欠陥を見逃す可能性があります。また、長時間の検査作業は作業者の疲労を招き、検査精度の低下を引き起こすことがあります。
機械検査
機械検査は、自動化された装置を用いてワイヤーハーネスを検査する方法です。機械検査は、精度が高く、一貫した検査結果を得ることができます。代表的な機械検査方法には、引張試験機や圧縮試験機などがあります。これらの装置は、ワイヤーハーネスの機械的な特性を測定し、規格に適合しているかを確認します。機械検査の利点は、信頼性が高く、大量生産に適している点です。しかし、初期導入コストが高く、装置のメンテナンスや運用にもコストがかかることがあります。
画像検査
画像検査は、カメラと画像処理技術を用いてワイヤーハーネスを検査する方法です。画像検査システムは、高速かつ高精度で欠陥を検出し、人為的なミスを減少させることができます。画像検査の利点は、微細な欠陥や複雑な形状の検出が可能であり、特に大量生産に適している点です。最新の画像検査システムは、AI(人工知能)技術を組み合わせることで、さらに高い精度と信頼性を実現しています。AIは、大量のデータを学習し、新しい欠陥パターンにも迅速に対応することができます。画像検査の課題は、初期導入コストがかかることと、システムの設定や調整に知識が必要な点です。
目視によるワイヤーハーネス外観検査の課題
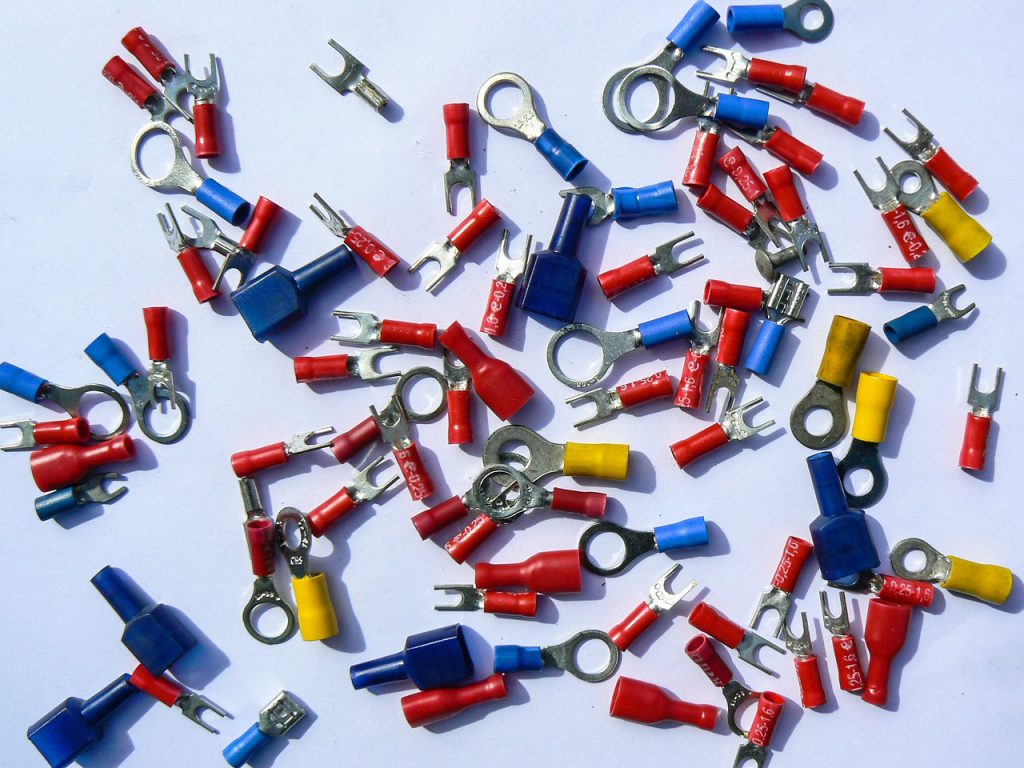
目視検査は伝統的かつ広く使用されている検査手法ですが、いくつかの課題があります。これらの課題を理解し、改善策を講じることが、ワイヤーハーネスの品質向上に繋がります。
作業者による誤判定
目視検査は作業者の経験と技能に依存するため、個人差が大きくなりがちです。熟練した作業者であれば高い精度で検査が可能ですが、未経験者や訓練不足の作業者では誤判定のリスクが高まります。また、作業者の体調や集中力によっても検査精度は変動します。これにより、検査の一貫性が保たれず、品質管理が難しくなることがあります。誤判定を減らすためには、定期的な教育や訓練、標準作業手順書の整備が必要です。
作業効率が悪い
目視検査は手作業で行われるため、検査に時間がかかります。大量生産の現場では、目視検査の速度が生産ラインのボトルネックとなることが多く、生産効率を低下させます。また、長時間の検査作業は作業者にとって負担が大きく、疲労やミスの原因となります。効率を改善するためには、作業者の休憩を適切に取り入れるとともに、作業環境の改善や検査工程の自動化を検討することが重要です。
ワイヤーハーネスの外観検査を画像検査で行うメリット
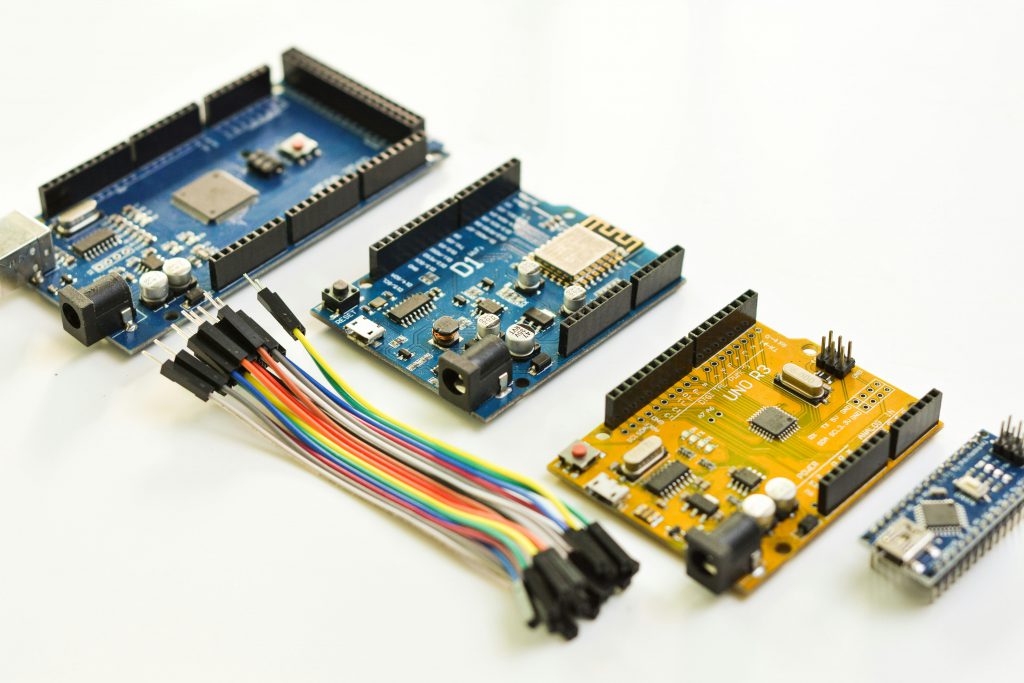
近年、AI(人工知能)技術の進歩により、画像検査がワイヤーハーネスの外観検査において重要な役割を果たすようになりました。画像検査の導入には多くのメリットがあり、従来の目視検査や機械検査を補完または置き換える手段として有効です。
検査精度の向上
画像検査システムは、高精度なカメラと高度な画像処理技術を使用しており、微細な欠陥や不良を検出する能力が非常に高いです。AIを活用した画像検査は、膨大な量のデータを学習し、常に検査精度を向上させ続けることができます。これにより、従来の目視検査では見逃されがちな欠陥を確実に検出し、製品の品質を保証することができます。
検査時間の削減
画像検査システムは、自動化されたプロセスで高速に検査を行うことができるため、検査スピードが大幅に向上します。従来の目視検査に比べて、数倍以上のスピードで検査を完了することが可能です。これにより、生産ラインのスループットが向上し、全体の生産効率が高まります。高速な処理能力を持つ画像検査システムは、リアルタイムでの検査が可能であり、即座に不良箇所を特定して修正することができます。
検査コストが低い
画像検査システムの導入により、長期的には検査コストの削減が期待できます。初期導入コストは高いかもしれませんが、検査作業にかかる人件費や時間を削減できるため、総合的なコスト削減が可能です。また、画像検査システムは24時間稼働が可能であり、休憩や労働条件に左右されないため、継続的に高いパフォーマンスを発揮します。これにより、投資回収期間が短縮され、コストパフォーマンスの高い運用が実現します。
まとめ
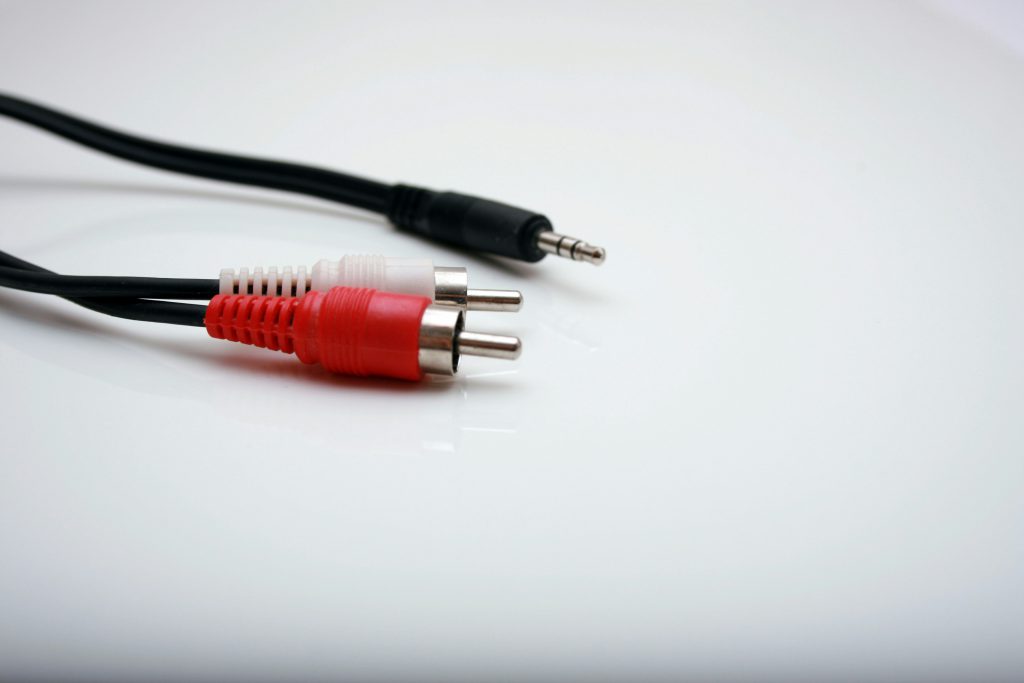
ワイヤーハーネスの外観検査は、製品の品質を確保し、信頼性を向上させるために欠かせない工程です。この記事では、ワイヤーハーネスの外観検査の目的から始まり、構成する部品、検査項目、検査手法、目視検査の課題、そして、画像検査のメリットついて詳しく説明しました。
ワイヤーハーネスを構成する主要な部品(電線、ハウジング、チューブ、クランプ・結束バンド、テーピング、端子)は、それぞれ特定の役割を担っており、各部品の外観検査は、電線の断線や絶縁不良、接続部の欠陥を早期に発見し、対策を講じるために重要です。
外観検査の手法には目視検査、機械検査、画像検査がありますが、それぞれの手法には利点と課題があります。特に目視検査には、作業者による誤判定や作業効率の低下といった課題がありますが、画像検査の導入によりこれらの課題を克服することが可能です。
PhoxterでもAI画像検査も含め、条件にあったハーネスの外観検査装置をご提案させて頂くことができます。
既存の光切断を使ったルールベース画像処理では過検知にお困りのお客さまが多く、当社でAIへの置き換え提案によりコスト、精度とも改善が見込めるケースが多いです。お困りごとがありましたら、まずはPhoxterまでお気軽にお問合せ下さい。