生産性向上や人手不足の解消といった物流現場の課題解決に、ロボットやソフトウェアシステムを用いた自動化が注目されています。この記事では、物流倉庫の自動化のメリット、失敗しないためのポイントや実際の導入事例を詳しく紹介します。
近年、新型コロナウイルスをきっかけとしたEC需要の拡大、宅配取扱個数の増加といった要因により、物流倉庫の取扱荷量は増加傾向にあります。また、「2024年問題」として知られている通り、トラックドライバーの労働環境の改善が社会課題となっています。ドライバーの年間労働時間を見直す必要があると同時に、物流現場の人手不足も深刻な課題です。物流業界の生産性向上・労働力不足の解消が急務となった現在、物流倉庫の自動化に注目が集まっています。
物流倉庫の自動化とは?
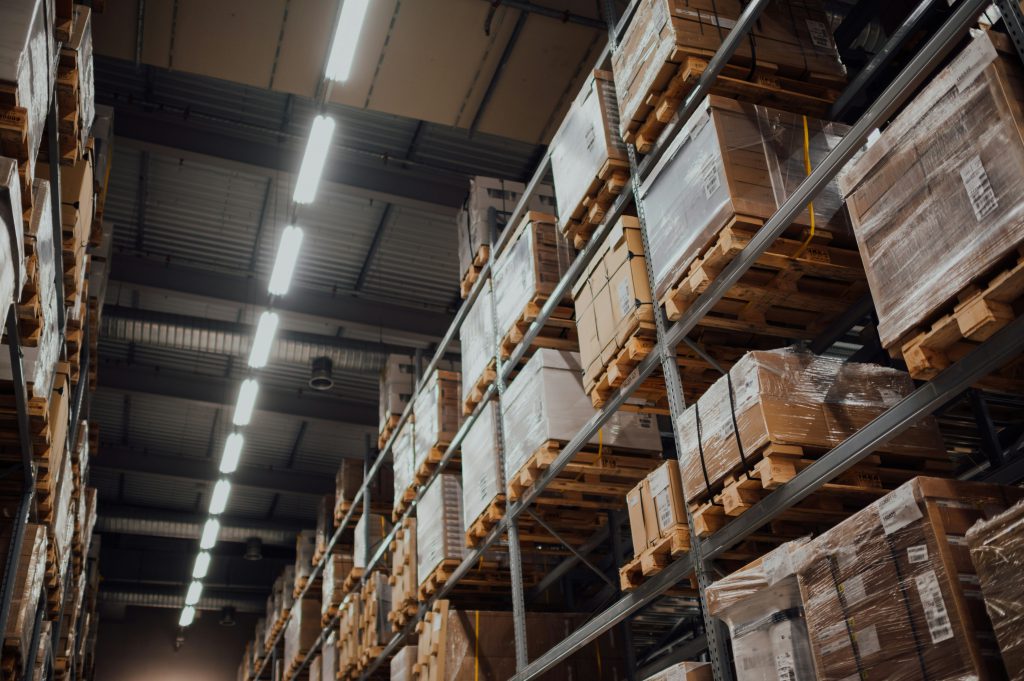
物流倉庫の自動化とは、商品の入庫、検品、保管、ピッキング、仕分け、梱包、出庫などの一連の作業をロボットやシステムに置き換えて自動化することを指します。昨今、作業の効率化や生産性向上を目的に自動化を進める企業が増えています。
物流倉庫自動化のメリット
はじめに、物流倉庫を自動化することで見込まれる4つのメリットについてご紹介します。
生産性の向上
倉庫の稼働時間は、その時々の荷量に左右されます。例えば、24時間体制での稼働が必要な場合、人員の確保や長時間労働・残業の発生といった問題がありますが、ロボットは稼働時間が限られないので、常に倉庫を稼働することができます。また、人手作業よりも作業ペースが早くなることが見込まれ、大量の物量に対応でき、生産性の向上に繋がるでしょう。
業務品質の安定
人が作業を行う限り、ヒューマンエラーはどうしても発生してしまいます。特に倉庫でのピッキング作業でのミスにより、発送先間違いや誤出荷が発生してしまうと、顧客との信頼関係が崩れかねません。自動化システムが作業者をアシストするような役割を担うことができれば、ヒューマンエラーを低減することができ、業務品質の安定に繋がります。
労働力不足解消・省人化によるコスト削減
EC市場の拡大により人手が必要な物流業界ですが、重労働にも関わらず低賃金といった傾向にあり、労働力不足が深刻な問題となっています。人の代わりにロボットや機械を導入すれば、上記のような現場の課題を改善することが可能です。また、省人化が成功することで人件費も削減できます。繁忙期に合わせて人員を新しく雇用する必要もなくなり、作業員の教育にかかるコストや求人コストも削減できます。
安全性の確保
危険物などの取り扱いが難しい商品を扱う場合や、高所に配置してある荷物や重量物を取り扱うことは、作業者にとって危険な作業となります。こうした作業をロボットに置き換えることで、従業員の安全性を確保することが可能です。
物流倉庫自動化の課題
物流倉庫を自動化することにはメリットがありますが、未だロボットやシステムの導入にはハードルがあるというのも事実です。具体的にはどのようなことが導入のネックになっているのか見ていきましょう。
導入・メンテナンス費用がかかる
導入コストの高さ、投資回収期間の長さが導入のハードルとして考えられます。ロボットや周辺機器の導入には数千万円以上かかる場合もあり、自動化して削減できるコストと自動化にかかるコストを十分に比較・検討しなければいけません。また、初期費用だけでなく、機器類のメンテナンスにも費用がかかってくることにも留意する必要があります。
業務体制の再構築が必要
倉庫内のレイアウトや業務手順、人員の配置など、システムに合わせてこれまでの体制を再構築する必要があります。その間も物流倉庫での業務は止められません。そのため、通常の業務と並行して、自動化による余剰人員の配置やレイアウトの検討などに大幅な時間を割かなければならず、忙しい現場において自動化を進める際のネックとなるでしょう。
物流倉庫自動化を成功させるためのポイント
物流倉庫の自動化は大きな投資になるため、無駄なコストが発生しないよう自動化の目的を明確にする必要があります。また、ボトルネックとなる工程の効率化だけでなく、その前後の工程との繋がりを意識し倉庫全体としての生産性向上を考えましょう。設備に使用する機器を複数のベンダーに依頼すると、機器同士やロボットとのインターフェース、制御が上手くいかないといったトラブルも発生しやすいので、慎重に検討する必要があります。
現状の課題、自動化の目的を明確にした上で倉庫稼働までのスケジュール策定を行いましょう。機器やベンダーの選定、ソフトウェアの開発やロボット納期を考慮してスケジュールを立てていくことが重要です。
参考:DX時代における物流倉庫自動化のポイント | デジタルエコノミー | 野村総合研究所(NRI)
物流倉庫を自動化するシステム・ロボット例
次に、具体的に物流倉庫自動化のために導入されるシステム・ロボットの例を紹介します。
立体自動倉庫システム
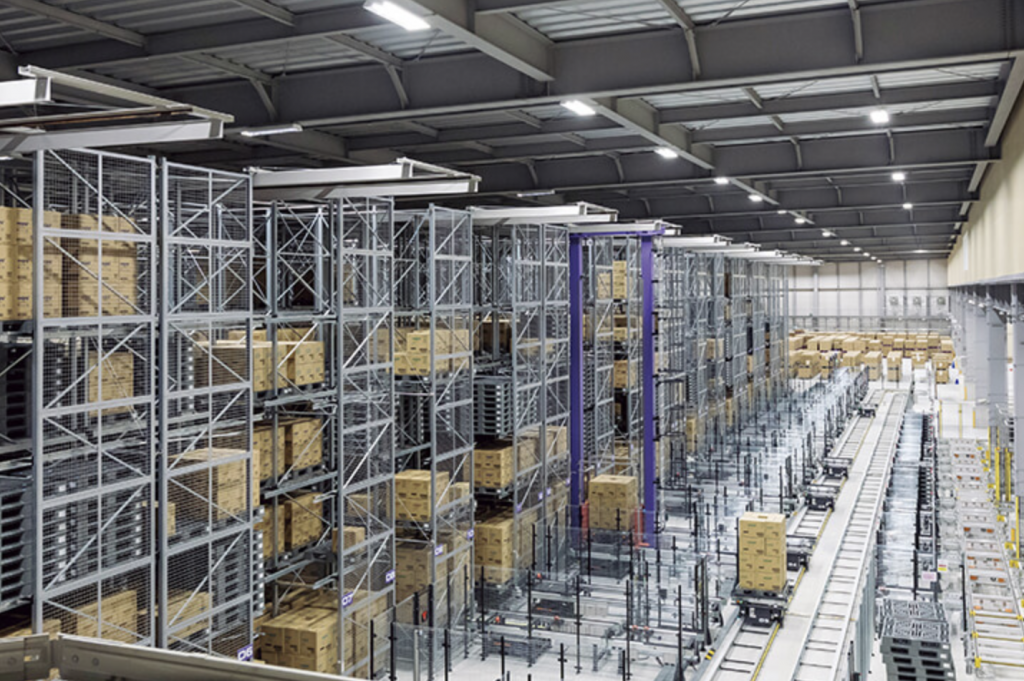
立体倉庫システムとは、縦に複数層積み重なった保管棚(ラック)に、搬送装置やシャトル台車が水平・垂直方向に移動して物品の入出庫や保管を行うシステムです。人の手が届かないような高層の場所にも商品を保管できるので、天井が高い物流倉庫のスペースを最大限に活かすことができます。立体自動倉庫システムは、パレットに原料や物品を積み込む「パレット式」のものとコンテナや段ボールを収納する「ケース式」のものがあり、様々な種類・形状の製品に対応可能です。
倉庫管理システム(WMS)
倉庫管理システムは、入出庫情報や在庫の数量といった情報を一元管理し、物流工程の効率化を促進するソフトウェアのことを指します。バーコードやカメラを用いて、在庫の照会・補充・入出庫の履歴管理・ロット管理などの在庫情報を自動で管理することができます。スマホやパソコンに情報が表示されれば、リアルタイムで商品情報を把握することも可能です。効率的な在庫管理が行えるほか、人為的ミスの低減にも繋がります。
検品システム
検品システムは、ハンディ端末やバーコードを使用し入出荷や棚卸しの検品作業を効率化するシステムです。バーコードリーダーで商品コードを読み取り、管理システムから出力した商品情報と照合して検品作業を行います。また、システムによっては、コンベアに設置した専用カメラで商品の賞味期限を自動認識することも可能で、搬送作業を止めることなく検品作業を効率的に行うことができます。誤出荷や検品ミスを低減でき、人員も減らすことができるといったメリットがあります。
参考:賞味期限自動読み取りによる、入出荷検品システムのご紹介(動画)
デジタルピッキングシステム
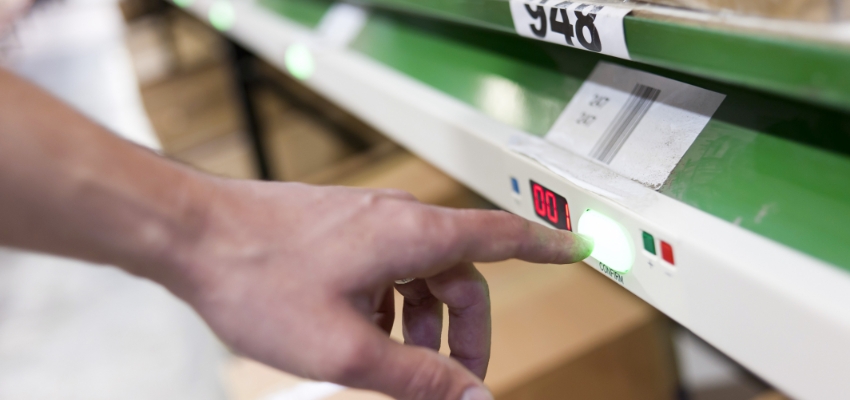
デジタルピッキングシステム(DPS)は、倉庫内でのピッキング作業を効率化するシステムです。従来は、作業者がピッキングリストを手に持ち、そのリストに従って商品のピッキング作業を行っていました。デジタルピッキングシステムでは、商品の保管棚に取り付けられたデジタル表示器に従って作業者が商品を取りに行くという仕組みです。そのため、リストの準備にかかっていた時間やピッキング作業自体の時間を短縮できるといったメリットがあります。商品名の見間違いや数量の読み間違いといったヒューマンエラーを防ぐ効果もあります。
自動搬送車(AGV・AMR)
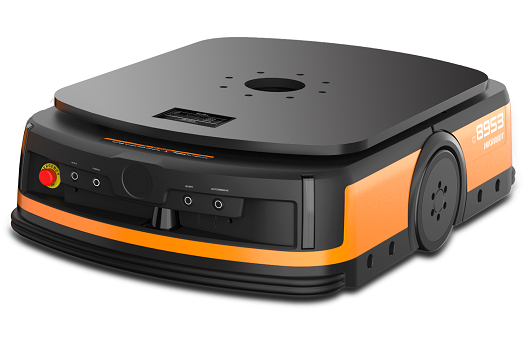
倉庫内の搬送作業を自動化するロボットとして、AGV(Automatic Guided Vehicle:無人搬送車)やAMR(Autonomous Mobile Robot:自立走行搬送ロボット)の二つが挙げられます。どちらも荷物を上に乗せる又は牽引することで倉庫内の自動搬送を可能にするロボットを指しますが、AGVは名前に「Guided」とある通り、磁気テープや2Dコードなどの誘導体に従って走行しています。誘導体(2Dコード、ガイド)から自己位置を認識して走行する為、環境変化に強く繰り返し精度が高い搬送が見込める一方、導入には倉庫内に誘導体の敷設が必要となります。AMRは、誘導体を使用せずセンシングにより周囲環境情報から自己位置を認識して走行しています。誘導体を必要とせず自律走行する為、立ち上げがスムースに行える特長があるといわれています。反面、センシングによる自己位置認識が重要となるため、周囲環境の変化に弱く、停止精度やスピードがAGVと比べて下がることがあり、目的によっては周囲に参照点(反射板や2Dコード、誘導テープ)を敷設する必要があります。最近ではロボットの開発が進み、用途や環境に応じて誘導方式を切り替えながら運用できるハイブリッドタイプも出てきています。どちらの誘導方式を使用するかは、目的や倉庫内の環境を元に判断する必要があります。
パレタイズ・デパレタイズロボット
パレットへの商品の積み込み、荷下ろし作業にはパレタイズ・デパレタイズロボットが利用されます。積み上げられた段ボールのコンベアへの搭載作業や、出荷前のパレットへの積み込み作業の自動化が可能です。重量物のハンドリングをロボットに任せられるので、作業者の安全性を確保できます。積み込みのパターンや向きを細かく指定することができるシステムもあります。川崎重工・ファナック・安川電機を始めとした各ロボットメーカーでパレタイズ適用のロボットの取り扱いがあります。
物流倉庫自動化の導入事例
最後に、上記で挙げたシステムやロボットを導入し、物流倉庫の自動化を成功させた事例をいくつか紹介します。
原料保管用に立体自動倉庫を導入
株式会社伊藤園神戸工場では、商品の原料保管に立体自動倉庫を導入しています。QRコードのスキャンで入荷した段ボールの実績管理が行われるので、人が伝票と現物をチェックする必要がなくなり、ヒューマンエラーがなくなりました。また、スキャンシステムにより一個単位で管理できるのも利点です。検品された原料はその後ラックで保管されますが、その投入・搬出作業をシステムで自動化しています。その結果、3名の省人化に成功しました。また、搬入指示はシステムから自動で払い出されるので、人為的なミスを無くなりました。原料を加工した後の半製品の包装・パレタイズもロボットで自動化されており、その後自動倉庫で出荷まで保管される仕組みを構築しています。
参考:【導入事例】㈱伊藤園様_複数荷姿保管用立体自動倉庫
自動倉庫への搬入作業をパレタイズロボットで自動化
愛知県名古屋市の製菓メーカーである春日井製菓株式会社は、パレタイズロボットの導入により自動倉庫への製品の搬入作業を自動化することに成功しました。商品はパレタイズエリアまでコンベアで運ばれます。コンベア上でQRコードを読み取り、それぞれの商品のパレタイズエリアに振り分けられます。パレタイズエリアでは、川崎重工のパレタイズロボットCP180Lがパレットに商品を積みつけていきます。1台のロボット毎に1日20パレットへの積みつけが行われているそうです。人手作業を無くしたことで、従業員の身体的負荷を低減でき、ヒューマンエラーも無くすことができました。
参考:導入事例:春日井製菓株式会社の生産エリアから物流までの自動化システム一本化 | 川崎重工の産業用ロボット
倉庫内の商品搬送にパレット搬送AGVを導入
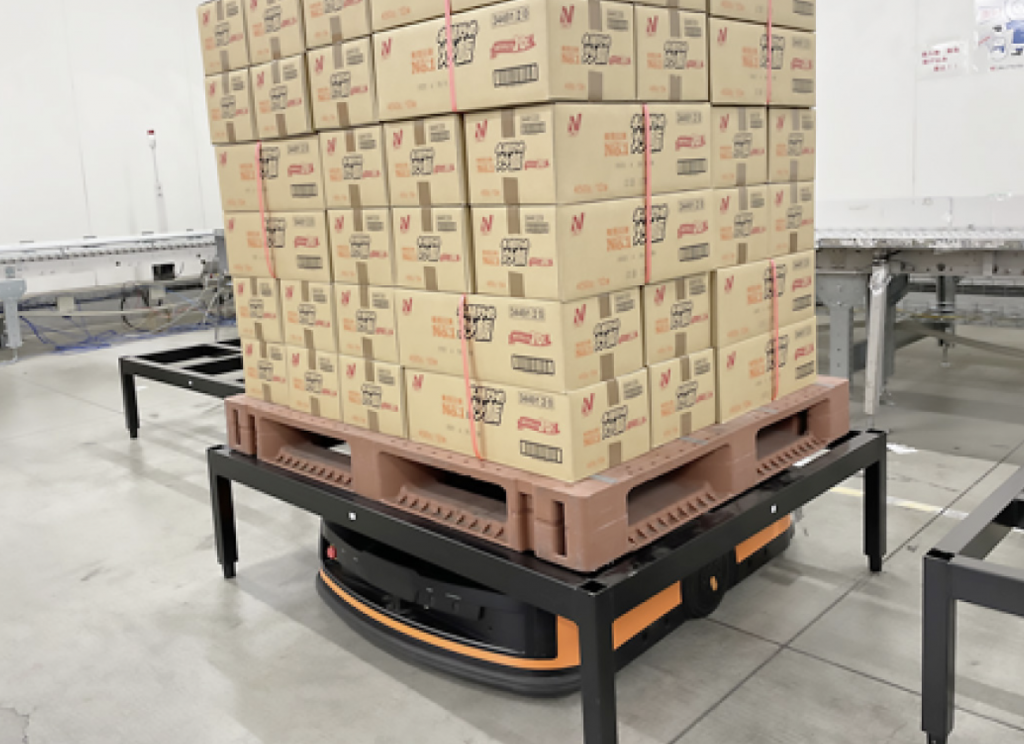
株式会社ニチレイ・ロジスティクス東北の仙台物流センターでは、冷凍食品の搬送にPhoxter製のパレット搬送型AGVシステムを導入しています。従来はフォークリフトで商品の搬送を行っていましたが、AGVを導入することで作業者の負担を大幅に軽減することができました。AGVを導入し現場作業の属人化を防ぐことで、昨今の労働力不足を補うためのソリューションにもなっています。
参考:パレット搬送型AGVを導入 | ニュース | ニチレイロジグループ
まとめ
物流業界では、物量が増加する一方で人手不足が深刻化しており、ロボットやソフトウェアサービスの導入による自動化の傾向が加速度的に高まっています。こうしたニーズに合わせて自動化技術も進歩しているので、専門家のアドバイスも活用しながら現場の課題に適したソリューションを検討していきましょう。現場の自動化を検討する際には、国内で2000台以上のAGV・AMRの導入実績がある株式会社Phoxterまでお問い合わせください。お客様の入庫から出庫までの流れを把握した上で、最適なソリューションをご提案することができます。